検品ミスの対策や誤出荷に悩む物流業界の方は多く居るのが現状です。検品ミスや誤出荷があれば顧客からの信頼が低下してしまうだけでなく、事後対応等、業務の負荷が増えてしまいます。そこで本記事では、検品ミスやご出荷が起こってしまう原因やタイミング、その対策等を解説していきます。ぜひ最後までご覧ください。
納品ミスが起こりやすいタイミングや原因
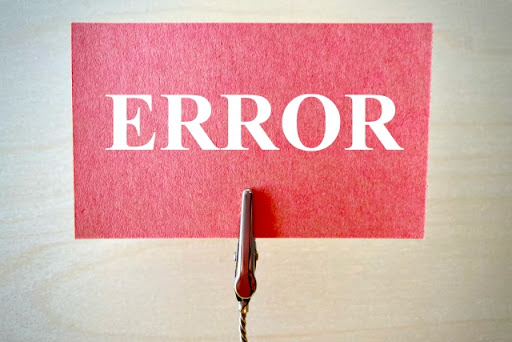
検品ミスや誤出荷等を行っていく上で、まずなぜそれらが起きてしまうのか、どのタイミングで起きているのかを知る必要があります。そこでどのような原因やタイミングで起きているのか具体的に解説していきます。
出荷指示
誤出荷や検品ミスを無くすことを考える上で、まず絶対になくしたいのがこの出荷指示のタイミングでのミスです。なぜならこのタイミングでミスが起こると、その後の検品やピッキングをいくら丁寧に取り組んでも、誤出荷を防ぐことができないからです。そのため、出荷指示のタイミングでのミスはゼロにするのが理想です。
出荷指示の中でも、注文情報を入力するタイミングが最もミスが起こりやすいタイミングです。数量の入力ミスだけでなく、企画やブランド違い等似ているアイテムが多くある場合や、細かい条件がある場合は特に注意が必要です。
上述したようにこのタイミングでミスが起こってしまうと、その後の作業でいくら対策を講じても、検品ミスや誤出荷が発生してしまうので、絶対にミスを防ぎたいポイントです。
ピッキングや仕分け作業
検品ミスや誤出荷が発生する原因として最も発生しやすいタイミングが、倉庫内での作業=ピッキングミスです。倉庫内の労働環境、作業員同士の相性、労働時間等の要因があり、作業の質が属人的なため最もミスが発生しやすいタイミングです。
ここでのミスを防ぐことで、検品ミスや誤出荷を大幅に減らすことができるので是非抑えたいポイントです。ピッキングの中でも、類似アイテムとのピッキングミスや数量ミス等、多くのミスが起こる要因があります。最もミスが発生するピッキング作業での改善方法等は、後ほど詳しく解説しているので、是非対策を参考にして見てください。
配送業務
出荷指示やピッキング作業が完了した後も、実は検品ミスや誤出荷が発生していしまう原因が潜んでいます。それは配送業務です。配送プロセスに関しても、人が行う作業の為人的ミスが発生する可能性があります。
その具体的な例として、発送伝票の貼り間違いやトラック積み下ろしミス等があげられます。倉庫には多くの荷物が届く為、発送伝票を一括で入力した場合、作業員は多くの配送伝票の束の中から該当の宛先を探すため、ミスが発生する可能性があります。
またトラック積み下ろしの際も、ドライバーは多くの荷物の中から荷下ろし等を行うため、ミスが発生します。これらのタイミングでのミスを防止する対策も予め検討しておく必要があります。
納品ミスを防ぐ具体的な対策方法を紹介
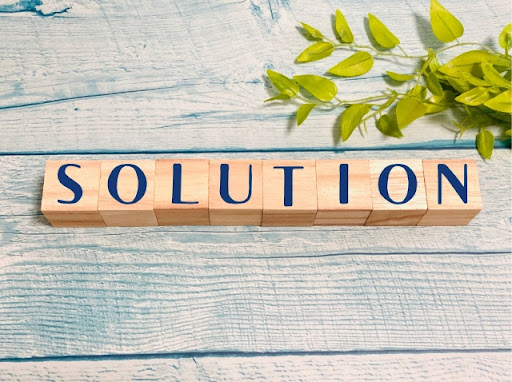
上述したように、検品ミスや誤出荷には様々な発生する原因やタイミングがあります。倉庫内での作業環境やルールを見直すことで、これらのミスを防ぐことができます。そこで、ここでは検品ミスや誤出荷を防ぐための具体的な対策方法を5つ紹介します。自社の業務の中で取り入れることができる対策があれば是非参考にして、導入を検討してみてください。
➀保管場所と情報共有の徹底
まず入荷した商品が正しい数量で、正しい場所に置かれているか確認することが重要です。また保管場所に変更があったりする場合は、その情報を社内で共有して全員の共通認識にすることでミスを予防することができます。また商品を保管する際は、SKU単位できちんと場所を定め、それらの情報を社内全員で共有することが重要です。
当然と思われがちな事ですが、これらの事を徹底的に行う事で、入荷商品を誤った場所に保管したり、誤った商品をピッキングしたりするミスをなくすという事は、見落とされがちです。この当たり前のことを徹底して行う事で、大幅に誤出荷を減らすことができると思います。
②作業手順の作成とルールの統一
倉庫内の作業等において、業務フローごとのルールを作成し、作業手順を統一化することが重要です。特に、作業員が手作業等で行うものは、作業の質やかかる時間が属人的で統一化されにくく、ミスが発生する要因となります。作業手順書を作成しルールを統一することも重要な対策法と言えます。
下記は作業手順の作成の例とそのメリットです。
・入荷作業手順の統一
入荷時の数量確認手順から商品保管ルール等、主に商品誤出荷の防止につながります。
・梱包前検品作業の作業手順の統一化
梱包前に行う商品確認や数量カウントルール等、主に商品誤出荷や数量誤出荷の防止につながります。
・梱包作業の手順統一化
梱包の際の作業手順やルール(1梱包ずつの作業を遵守・卓上に複数の梱包物はおかない)等、主に宛先誤出荷の防止につながります。
作業手順の統一化を行う事で、作業手順やルールを作業員全員の共通認識にすることができ、新人スタッフの育成の際にも、教える内容を統一することができ、教え方の違いによるミスの発生を防ぐことができます。
③余裕のある作業スペースの確保
作業を正確に行う為には、余裕のある作業スペースを確保する必要があります。
特に元旦や年末のセール等の繁忙期で作業の件数が多くなる時期は、作業員の人数も増える為、あらかじめスペースの確保を行う事で、ミスの防止に繋がります。
その為にも、日ごろから作業員全員が作業スペース周りをきれいにすることを心掛ける事も忘れずに行う必要があります。
④ハンディターミナルを設置する
昨今では商品にバーコードがついている場合が多いです。その際には、ハンディターミナルを導入しシステムを活用したピッキングが有効です。
ハンディターミナルやスマートフォン等にピッキングする商品が保管されているロケーション番号を明記します。
ピッキングする際に商品のバーコードと棚のバーコードを読み込むことで、ミスがないか確認することができるので、正確なピッキングが行えます。
その他にも、複数の出荷先の商品をまとめてピッキングできるマルチピッキングカート等の活用も作業効率と出荷精度の向上に繋がり、ミスを防止することができます。
⑤アウトソーシングする
上記のハンディターミナルやシステムの導入が難しそうな場合には、アウトソーシングを検討する事もおすすめです。やはりミスを減らしたり、精度の向上を目指すうえで、システムの導入等は避けられない場合もあります。
そこで、多くの実績や長年のノウハウが蓄積しているプロにアウトソーシングすることで、誤出荷や検品ミス等を防止することができる他、メイン業務にリソースを割ける等メリットも多くあると思います。
検品ミスや誤出荷等のミスが目立つ場合は、是非アウトソーシングも検討してみてください。
まとめ:原因を把握して対策を講じれば、納品ミスは防げる
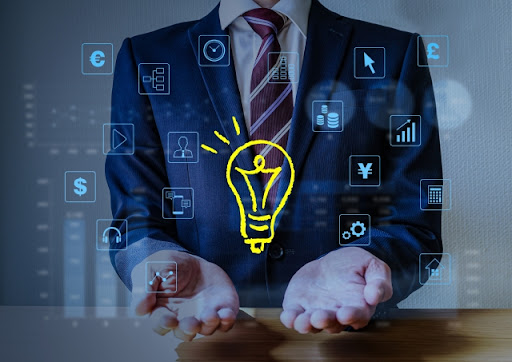
昨今のEC市場の拡大やパンデミック流行による生活様式の変化により、物流のニーズは急成長中です。その中で売上拡大を考える場合は、やはり顧客との信頼関係の構築は必須になります。その為に誤出荷や検品ミス等は極力起こしたくないものです。
仮にそのようなミスが起こってしまった場合も、本記事で取り上げた観点を参考にして、原因の究明を行ってみてください。また見つかった課題に対して、本記事で具体的に紹介した対策方法を導入することで、改善を行えると思いますので、是非参考にしてください。最後までご覧いただきありがとうございました。